Offset Onset
Delicious, glorious, happy gloom. A gloom so wet in London they’d call it drizzle. And I out into it for back-to-back yesterslack and this AM rikes. Desirement – build to a 5 day a week program. So far, so slack.
Dressed for deluge, although this was not in the forecast, but every other year or so, since my time here, there’s been a thunderstorm in July.
Pried at knife-point Wildman out of his newly organized shop/garage for a jaunt to Watsonvilled and Jackel Hardwood. Wildman is so newly organized that not only are all his power tools readily available, not only is his estimable lumber yard sorted by color, age, continent, tone, grain, length, likelihood of the Feds raiding, and thickness (well, maybe not by thickness), but not only can he move without falling into the table saw, he can actually get his car in the garage. In California. Yes.
The happy gloom disperses by Watsonville into depressing, bright sunshine. Bah.
My lumber pile is not the cornucopia that is Wildman’s, but it is full on the rack so I’ve no intention of procuring. Wildman’s there for some alder. And then it happened. Luv at first blight.
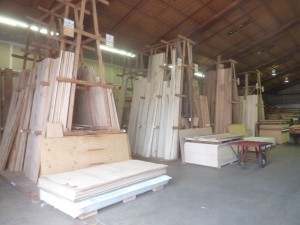
Jackel Hardwood is like any temple – much to be worshiped, and also like any mythos, there’s a price to be paid.
Cherry, cherry backer board. A 12 foot length more than a foot wide and ½” thick. Cracks, defects sure. Sure I’ll make the best of it. I’m smitten. On backer board, they rip you a price – in this case $3.50 per – for linear feet, so the $42 equated to $6.61/board foot. Harvey Un-approved.
The saving slack is that I’m paying for them to re-saw it down to the ½” thickness which is ever so more useful here at JohnsonArts than 4/4 or thicker which I’d have to re-saw – for which I haven’t the bandsaw ability.
Wildman nails some poplar instead of the alder, and a length of walnut backer board – jews the guy down $5. Harvey Approved.
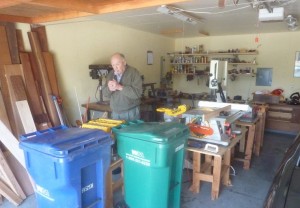
Here’s the Wildman violating OSHA regulations about smoking in a combustible environment; note the organization – and trust me, it IS organized compared to the compost heap it once was….
And way the by, Wildman is doing well for a young sprog of almost 83, his legs are stronger and his outlook is bright. He’s looking forward to a two-week September urlaub with his kids to Brit Columbia. Waugh!
FOOTDAY –
As in the game is a …
It’s those oak wine barrel staves.
The Design Bureau has promulgated half a dozen concepts from chairs to bookcases to a flying pterodactyl dressed like Spiro Agnew – all nixed.
And then it happened, as it always does, I had a drink. No, no, no, no, no….. I mean yes, yes, yes, yes, yes, but that’s not what happened that always does. What happened that always does is that some spark ignites out of the Void of Design Concept Nothingness and there It IS.
I usually try mightily to find fault with it, or raise procedural and engineering reasons why it’s WRONG.
And this is a good thing because it challenges that idea as much as the idea challenges me; and burns down limp dick, unappealing, pedestrian all-too-normal themes.
Couldn’t shake this one even though it presented, at its emergence, significant engineering challenges.
Which I like hating that I like.
The Idea: a sort of whirling, radial-offset set of shelves supported by and enclosed in a tripod of barrel staves, convex side out.
Each of the seven shelves is 30 degrees offset to the shelf above and below and so from top to bottom the shelf pattern corkscrews 180 degrees. I would have liked for a full 360 degrees, but alas, the length of the barrel staves only gives me about 80 cm top to bottom into which to insert seven shelves, that clearance dictates about 10 cm apart, separated by dowels, each being like a small table standing on the one below, but with more than four ‘legs.’
I have no idea what I’m doing. Which is where I feel most comfortable. And in cases like this, I find working up some scale drawing not only helpful, but the drawing process itself both allows and causes a deeper penetration into the project unknowns than standing around scratching my nuts.
First was a half-scale profile view estimating the curve of the stave tripod inside which the whirling dervish shelves shall whirleth. Then a plan view (as in looking at the thing from above) that shows the 30 degree offset around a common center of mass, which in this case is the geometric center.
This plan view was not only a guide to how the shelves would look, but will aid in determining dowel position. Somehow. Yes, I’m feeling my way through this like a night SCUBA dive without a flashlight.
There’s sufficient bamboo flooring on Woodpile #41 to make all the shelves, which are 18 cm wide and range from 20 – 88 cm long.
The bottom shelf is worrisome. As the bottom shelf, it will naturally attract the largest and most massive items. About 40ish cm of cantilever either end is a problem. Under-shelf bracing is a possible solution.
But the main known unknown is how to align, top to bottom, the center of mass of each shelf. The slightest deviation will show as a visible wobble when the thing is rotated. Even at sub-Mach speeds.
Knowing this is an unknown and not knowing how to make the fix a known known, I turned to the staves. For reasons completely unknown to me, I immediately formed an alder disc about 18 cm in diameter and about 5 cm thick to which the upper ends of the staves will be – in some manner not now known – affixed. The lower ends will be connected to each other radially in the center of the tripod by …. something to which the lazy susan on which the shelves rotate will be lashed. Really.
Sanded out the arc of the alder disc contour on the upper ends of the three staves, then, leaving an upper lip of about 1.5 cm undercut the disc so that the stave ends wouldn’t be naked. I should NOT have used a ½” upcut spiral router bit. Made the undercut fine, but at the price of severe burning, the bit just isn’t designed to hog out wood on its sides, but it was the only bit I had large enough for the task. Should have used the table saw. Learning.
I leave all the known unknowns to that fruitful, productive unconscious which is the dream state.
DREAMSTATELIVEDAY –
Everything going my way: delicious coastal gloom, a compliant knee, and the stock market drifting flotsam toward my beach.
Aimed and achieved a 50 minute rike, although not with the 8 pound dumbbells, save that for Slackterday.
Thus ennobled, must create – down the secret tunnel concealed inside my 80 foot tall Buddha icon – to The Shop and the Whirling Dervish Project.
There’s no more clarity on the project known unknowns, and so we proceed with that which is known, which is lam out the nearly 18 cm wide swaths of bamboo flooring, courtesy of Curtis’s hot water heater leaking lo these many cycles ago, into sufficient lengths, then cut to the 16, 32, 44, 56, 66, 80, and 88 cm shelves.
And that was the easy part.
Somewhat less not easy was the product of last nights/morning Midnight Study Hall which floated this idea: could not the ardent artisan form paper templates of the dowel hole drill pattern which would obviate the finding of shelf center of mass?
It could, it might, I would, I will.
Given the 30 degree radial offset, there’s a predictable amount of overlap lower to shelf above. Once drawn out on a paper template, the desirous locations of dowel holes become revealed.
Yet all is not full sails freshet from astern and calm seas ahead
The Chief Known Unknown is how to establish structural integrity with the chosen shelf to dowel to shelf design.
Loading the shelves with kachinas, anvils, beer mugs or Spode puts the dowels in tension, not so much the dowels but the dowel tenon joints. I can screw in from below a washer-head screw which will secure that dowel joint, but what of the upper? Will Gorilla Glue save the day. Tune in for our next episode of JohnsonFrets!
We interrupt our regularly scheduled program to bring you this special case of beer. Well, it was The Professor who brought the half case of Guinness and half case of Lag.
Philosophical inquiries commenced. Thesis proposed. Grog quaffed.
He departs all too soon, but with the dovetail box and glad I am to have it off the bench for as you well know, there’s never enough space.
DOWELDAY –
But not until after the weekly provisioning run to Krasnoyarsk.
Okay, okay, it wasn’t Krasnoyarsk, it was more like Marina, and I wouldn’t have gone that far if another gallon jar of kim chee wasn’t mandated. Since it takes a week and a half on the North Promenade to properly …. shall we say, mature the manky cabbage, once the extant jar is half empty, it’s time to procure its follow-on.
And so it was after the usual negotiations at Trader Joe’s for the Dutch nepenthe. And right glad I was to attend Grocery Cheaplet in Marina as they had on the mongo-sized jar of Heifetz dill pickles I fancy.
From there to Home Desperationpot for 7 hardwood dowels. I wanted oak, I didn’t get oak. I got what they had, whatever it was but since the intended struts for the Whirling Dervish were only to be about 11 cm long, I almost could have used Q-tips. And the whatever they had was so affordable I got more than I needed as dowels here are in frequent need.
The lovely coastal gloom cloaks my movements thence to CVS for the yearly contact lens/mind control fluid and to Ka-Nob Hill for this summer’s first peaches.
After luncheon – endangered bluefin with a glace of Rhone truffle sided with illegal unpasteurized Pyrenees camembert served on hollowed out elephant tusk on a sea otter tablecloth– it’s down the hayloft rope to The Shop and today’s fun. If Fun There Be….
Last night’s Midnight Design Review acknowledged the tenon tension issue, and in spite of being a committee, from which little good can come, resolved simply to ignore the issue, thus rendering it a non-issue. Not unlike the Florida State Department of Education with a stroke of the bureaucracy inspiration simply by fiat declaring that no, that wasn’t a C grade, a C Grade wouldn’t be sufficient to demonstrate institutional progress in qualifying for Federal funding, it’s a B!
Yet, another arose.
I intend that this design, this weight seat on the floor, specifically, the weight of the Whirling shelves will rest upon a centered ball-bearing lazy susan and this lazy susan will rest upon a … something – that also links the three legs near the floor with some connectors – and that something will repose on the floor.
Good enough, until you move the thing, pick it up.
Picking the dingus up will impart untoward downward stress on the something linking the three legs to which the ball bearing lazy susan is affixed. Since the connectors are horizontal, a downward force, inherent in picking the whole thing up, causes immense strain on the connector joints, legs and center something. Collapse would be the result.
What to do?
There’s probably a dozen methods, but here’s the one the Midnight Design Bureau chose: Drill through and countersink from the top of the cap to which the three legs are joined sufficient indentation for the head and some maybe bearing a big, long wanking lag screw that penetrates through the cap and into a …. something , likely a big, suitably long, wanking dowel which is firmly lashed to the very top shelf of the Whirl. Screwed into the something affixed to the top shelf just so, so as not to impede rotation, the head of the lag screw will carry the load of the entire set of shelves when the entire dingus is lifted.
Maybe.
All this left to the imponderable future as the task now is make the 30234237 dowels with tenons. Okay, okay, it’s more like 30 dowels cut to 11.8 cm with each end 0.8 cm in reduced from ½” diameter to 5/16” tenons.
Since there’s no Real Guy here to tell me how it’s Really Done, I do this: On the table saw clamp the square so that the dowel rides against it just at the longitudinal center line. I set the fence so that pushing a dowel against it will cut a tenon shoulder, once the blade is raised, 0.8 mm. Then, I sneak up on the blade height by raising it an hour on the clock until the rasted out diameter of the tenon is righty-tighty into a test 5/16” hole.
As Mr. Left Pinky is deucedly close to the Carbide Teeth of Violent Trauma, fear factor runs off the scale.
And it’s boring. Really Boring. Repetitive tasks such as this evoke a wandering mind. And THAT is danger. Trust me.
Even so, I lam out enough 5/16” tenons at 0.8 mm for the project, and that was the EASY Part.
What’s not so easy is transferring the hole patterns of the lower shelf, we’ll call the bottom shelf shelf #7, to the underside of shelf #6. But with a paper template, I stand a chance. After marking the drill site holes on the upper face of shelf #7, I flip the template, center it using a pushpin, align it to the 30 degree offset and then using an ice ax, mark the drill site on the underside of shelf #6.
It works, but not with the precision you’d like. For a production run, I’d develop masonite templates. Or out-source the thing to Taiwan.
Holes are drilled, dowels are dry fit, the thing takes shape.
And in slackrospect, the use of bamboo flooring was a tactical blunder for two reasons
1. there’s a tongue and groove split down the middle of the 18.9 cm wide shelf(s).
2. the underside is corrugated, which for flooring allows channels for the contact cement.
Two of the shelves, in dry fit, broke along the seam, and the choice of dowel holes, which was done entirely without consideration of the undersurface corrugation, leaves some aspect of some dowel shoulders up in the air.
Yet, I chose the flooring because it was handy, about the right thickness and I had plenty of it.
Learning.
Dry fit the entire thing, finesse the dowels, glue up the split shelves, glue together shelves #6 to #7 and move toward the tripod.
Pre-drill and countersink the upper ends of the three barrel stave legs, mark the corresponding sites on the alder top cap, then pre-drill it.
Those barrel staves, on the inside have a gorgeous lurid purple and on some caked on residue. I like the purple color, but can I scrape off the crusty sugar residue.
I can.
Tomorslack, if Tomorslack There Be: Assemble the shelves, test-fit inside the dry-fit tripod and then suss out what to do next.
Some people will be mowing the grass, others going to Costco, others still paying for manufactured ‘entertainment’…. Not me.
GLICKDAY –
The fourth rike of the week was mandated, got as far as the warm up before that spinal ‘glick’ resulting from catching the baby thrown out the 28th story window of the Holman Building invoked the better part of valor. I’d like to tell you it was catching (no glove, bare handed) a baby, I really would like to tell you that, but it actually resulted from bending over the fetid laundry pile. So it goes.
Go I to Le Shoppe via the Metro – was going to slack the day off from usual slacking, but Elmer would have made the shop if he could.
Unclamp yesterslack’s riven flooring, screw in on the underside of the topmost shelf a metal plate which will stabilize the thing and form the foundation of whatever it is that makes up the dif between the top shelf and the underside of the roundel, top of the tripod.
Glue up shelves 7 – 6 to 5, turn to the tripod.
Probably there’s a better way to do this, but since I didn’t know what it was, I screwed the three barrel staves to the top roundel and set the rickety thing upright. Barrel Stave #1 seemed 5 cm too short, but I quickly (sort of) realized that rounded surface where the barrel stave met the roundel could be delicately adjusted (belt sander) to finesse the angle of slacktack.
Doing so on all three staves – one out the bottom of the joint, the other two a little off the inside top – brought the ‘legs’ into approximately the same approach radially as measured from the footprint. It is now the function of the lower connectors – which will span the near-bottom of the ‘legs’ to the center something on which the lazy susan will affix to unify and stability the structure of the tripod.
Either end of the staves some with the copper’s handiwork: the insets which secure the barrel top and bottom. Waterproof …. well, wine-proof. You don’t need me to remind you what a marvel of woodworking is a barrel; once as ubiquitous as today’s grocery bags and just as plentiful, yet in the main hand-crafted, fluid-tight, structurally sound.
So I want to retain every aspect of the stave I can, hence trying to form the stave end of the lower connectors to the config.
Suddenly, everything changes.
Up pulls the lux mobile of The Browns bearing a redwood outdoor lantern I’d ‘fixed’ years ago. It’s aged and degraded and needs attention, which I give it.
Also given attention are two brews borne by The Brown who does not walk off to the village.
Deschutes Chainbreaker White IPA – fruity, buoyant and cheerful – an handsome summer under the pool umbrella beer
Saranac High Peaks Imperial IPA – Drinkable, yet 20% of the mojo an imperial IPA ought to seize your palate with
The nobles depart leaving me nothing but barrel staves, insufficient joinery, but wispy inclinations toward future slackcess.
No comments yet.